Henschel HS 12 HK
Nun komme ich zu einem Projekt, das noch nicht fertig ist - mein LKW Henschel HS 12.
Den Henschel habe ich Ende 2016 von einem guten Oldtimer-Kollegen in Sonnenbühl abgekauft. Er hatte den LKW schon ein paar Jahre zuvor in Hechingen vor dem Verschrotten gerettet. Er wollte ihn selber restaurieren, hatte aber zu wenig Zeit, da er zu diesem Zeitpunkt noch vier andere Oldtimer-LKWs hatte. Er stellte ihn somit vorerst nur in seiner Halle ab.
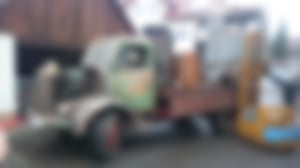
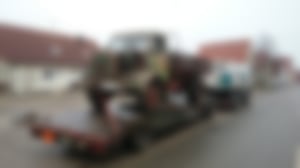
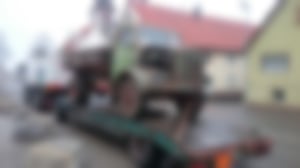
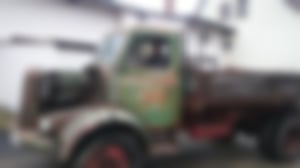
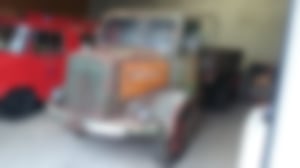
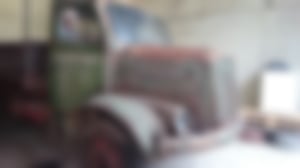
Nachdem ich den Henschel bei mir Zuhause abgeladen hatte, habe ich zuerst eine Bestandsaufnahme gemacht. Er war fast komplett. Nur die Scheibe an der Fahrertüre war eingeschlagen und war nicht mehr vorhanden. Ich habe mir alle Unterlagen über diesen LKW besorgt, die ich bekommen konnte. Bevor ich den LKW zerlege, versuche ich ihn wieder fahrbereit zumachen, damit ich testen kann, ob alles funktioniert. Bei den Bremsen habe ich zunächst mal einen neuen Bremszylinder für das rechte Vorderrad gekauft und eingebaut sowie die Bremsbacken wieder gängig gemacht, damit ich bei meinen Fahrversuchen wenigstens mit einem Rad bremsen kann. Den Motor (einen Reihen-6-Zylindermotor) habe ich zunächst versucht von Hand durchzudrehen, was gut funktionierte. Nun spendierte ich ihm ein neues Öl. An der Einspritzpumpe habe ich schnell erkannt, dass sie keinen Druck aufbaute. Ein guter Freund, der gelernter LKW-Mechaniker ist, hat mir dann an einem Abend ca. 4 Stunden lang geholfen, die Pumpe wieder gängig zu machen. Anschließend haben wir einen Kanister mit Diesel angeschlossen und versucht die Kraftstoffanlage zu entlüften. Zuvor habe ich den Anlasser provisorisch an zwei Batterien angeschlossen, da der Anlasser 24 Volt benötigt, so dass wir den ersten Startversuch machen konnten. Nach kurzem Drehen des Anlassers sprang der Motor auch schon an. Aber er qualmte so stark, dass die ganze Werkstatt vernebelt war. Wir dachten, dass der Motor nicht mehr so stark qualmen würde, wenn er mal länger laufen würde und mal wieder richtig warm wird. Aber zu diesem Versuch musste ich zunächst das Kühlsystem dicht bringen. Dazu habe ich erst neue Kühlerschläuche gekauft und eingebaut. Vor dem ersten Fahrversuch habe ich dem Hauptgetriebe, Nebengetriebe und der Hinterachse auch ein neues Öl verpasst. Nun stand dem ersten Fahrversuch nichts mehr im Weg. Ich war sehr positiv überrascht, dass alles so gut funktionierte. Das Hauptgetriebe ließ sich gut schalten. Nur das Nebengetriebe konnte ich nicht testen, da ich die elektrische Anlage noch nicht instandgesetzt hatte und das Nebengetriebe über ein Magnetventil bei einem Lastwechsel geschaltet wird. Aber das konnte ich zu einem späteren Zeitpunkt noch testen. Als ich den Motor für einen weiteren Fahrversuch startete, war die Werkstatt wieder sehr schnell voller Qualm und ich fuhr schnell ins Freie. So fuhr ich aber zu schnell los und wartete nicht ab bis genügend Luft in der Bremsanlage war. An der ersten Kurve wollte ich bremsen, aber sie funktionierte nicht, da in dem LKW nur eine reine Luftdruckbremsanlage verbaut ist. Zum Glück ging alles nochmals gut und es ist nichts passiert. An der Wasserpumpe habe ich dann festgestellt, dass sie etwas undicht war. Nun habe ich neues Öl auch noch in die Hydraulikanlage eingefüllt, so dass ich den Kipper ebenso testen konnte. Er funktionierte gut.
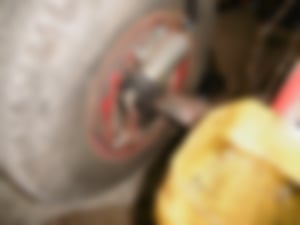
Endlich konnte ich mich an das Zerlegen des Henschels machen: Zuerst schraubte ich die Motorhaube und die vorderen Kotflügel ab, danach die vordere Stoßstange. Aber ich kam dann schnell mit meinem vorhandenen Werkzeug an die Grenzen, so dass ich mir größeres und schwereres Werkzeug zulegen musste. Als der Henschel komplett zerlegt war, habe ich alle Teile zum Sandstrahlen gegeben. Nach dem ich die Teile zurückgeholt hatte, habe ich sie zunächst mal nur grundiert.
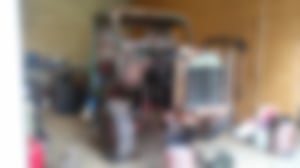

6 weitere Bilder
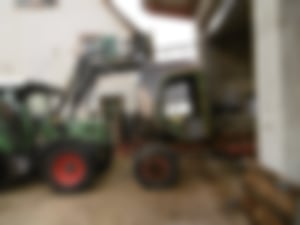
Nun machte ich mich ans Zusammenbauen des Rahmens. Zum Glück hatte ich vorher auch mehrere eigene Zeichnungen des Rahmens gemacht, da meine Fotos nicht immer alles so zeigten wie der Rahmen wieder zusammengehört. Nach dem Zusammenbau habe ich den Rahmen nochmals grundiert und dann lackiert.
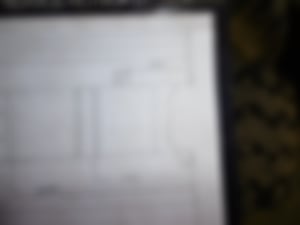
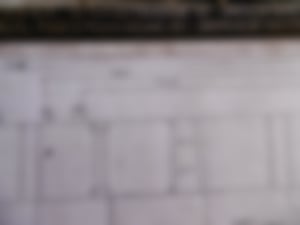
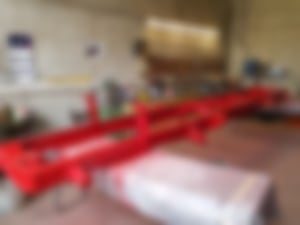
Die Federblätter habe ich zunächst an den Innenseiten eingefettet und dann zusammengebaut. Dabei halfen mir wieder Zeichnungen, die ich beim Zerlegen selbst gemacht hatte. Nun konnte ich die kompletten Federn nochmals grundieren und lackieren.
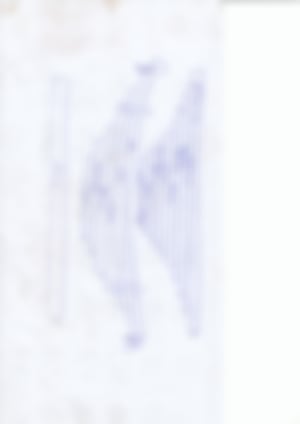
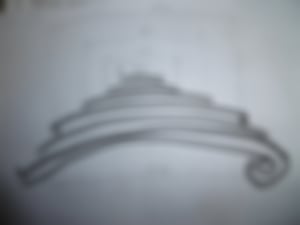
Nun wollte ich an der Hinterachse neue Dichtungen an dem Differenzialgetriebe zuschneiden. Als ich den Deckel öffnete, entdeckte ich jedoch Sand im Getriebe, das wohl vom Sandstrahlen herkam. Bevor ich die Hinterachse zum Sandstrahlen gegeben habe, hatte ich versucht, die Achse abzudichten. An den Seiten habe ich extra Hülsen angefertigt, aber leider hatte ich die Gewindelöcher, die für die Bremshebel in der Achse verbaut sind, nicht abgedichtet, denn ich dachte es seien Sacklöcher. Aber wie sich jetzt herausstellte, waren es leider doch keine Sacklöcher und es kam der Sand beim Sandstrahlen in die Achse. Nun musste ich die ganze Achse zerlegen, damit ich den ganzen Sand aus der Achse entfernen konnte.
Nach dem Zusammenbauen des Differenzials habe ich noch neue Dichtungen angefertigt und neue Wellendichtringe in die Achse eingebaut. Nun konnte ich die Hinterachse nochmals grundieren und lackieren.
In der Zwischenzeit verschickte ich die Bremsbelag-Halter nach Nürnberg, um sie neu belegen zu lassen. Leider ging beim Transport ein Halter verloren. Die Deutsche Bundespost sträubte sich sehr dagegen, mir den Verlust zu begleichen. Erst als ich mit dem Anwalt drohte, haben sie mir das Geld erstattet. Ein neuer Halter habe ich bei Arno Fries kaufen können. Nun konnte ich die Bremsen alle wieder zusammenschrauben und an die Achsen anbauen. Die Stoßdämpfer habe ich neu gekauft. Dann schraubte ich die Achsen an den Rahmen.
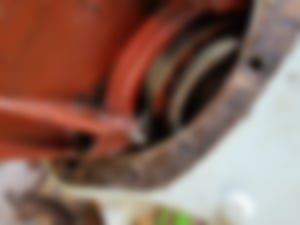
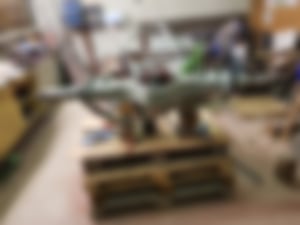
4 weitere Bilder
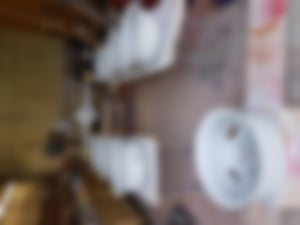
Nun ging es an den Motor: Hierzu konnte ich in der Nähe einen Ersatzmotor kaufen. Dieser wurde vor ca. 20 Jahren in einen Schuppen gestellt, weil der Vorbesitzer mit dem Motor ein Notstromaggregat bauen wollte, aber die Steuerung nicht hinbekommen hatte. Der Motor war noch am Rahmen mit dem Kühler verbaut. Ich versuchte jetzt den Motor wieder zum Laufen zu bringen. Zuerst habe ich versucht den Motor von Hand durchzudrehen. Danach habe ich das Öl gewechselt. Die Einspritzpumpe war leider sehr fest, so dass ich sie zerlegen und alle Teile im Ultraschalbad reinigen musste. Nach dem Zusammenbau konnte ich den Motor erstmals wieder starten. Aber leider lief er nicht auf allen Zylindern. Als ich den Deckel von der Einspritzpumpe öffnete, sah ich, dass ich beim Zusammenbauen einen Fehler gemacht hatte und deshalb am zweiten Zylinder kein Kraftstoff ankam. Der Fehler war schnell behoben. Der Motor lief nun auf allen Zylindern und er qualmte nicht so wie der Originalmotor. So beschloss ich, den Ersatzmotor herzurichten. Den Motor habe ich komplett zerlegt. Nur die Kurbelwelle habe ich im Motorblock drin gelassen.
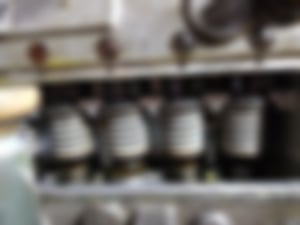
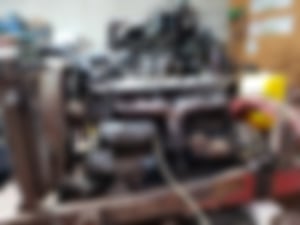
5 weitere Bilder
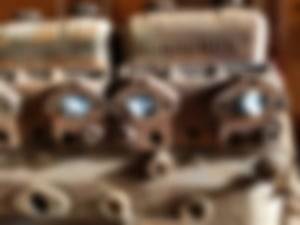
Nach dem Reinigen und Lackieren habe ich den Motor wieder zusammengebaut. Neue Zylinderkopfdichtungen kaufte ich in der Nähe. Die Ventildeckeldichtungen musste ich selber machen. Nun konnte ich den Motor in das Fahrgestell einbauen. Als ich den Kühler einbauen wollte, passte dieser nicht. Das Lüfterrad war zu hoch. Beim genauen Nachschauen habe ich festgestellt, dass im Ersatzmotor eine andere Wasserpumpe verbaut war. (Der Ersatzmotor war in einem Frontlenker LKW verbaut. Aufgrund dessen schmaleren und höheren Kühlers war dort eine andere Wasserpumpe verbaut.) Nun baute ich die Wasserpumpe vom Originalmotor ab. Aber sie war ja nicht mehr ganz dicht, weil im Gehäuse ein Riss war. Den versuchten wir zuzuschweißen. Da das Gehäuse jedoch aus Grauguss bestand, mussten wir es erst aufheizen, dann schweißen und danach wieder in Asche langsam abkühlen lassen. Aber leider haben wir so das Gehäuse nicht dicht bekommen. Danach habe ich das Gehäuse mit Flüssigmetall abgedichtet. Mit der alten Wasserpumpe passte auch der Kühler wieder rein. Nun verbaute ich noch neue Kühlerschläuche. Den Kraftstofftank habe ich ausgebeult und neu lackiert. Die Kraftstoffleitungen bis zur Einspritzpumpe und zurück habe ich neu angefertigt und eingebaut. Nun entlüftete ich noch die Kraftstoffanlage. Der Motor läuft wieder schön rund (ca. 15 Stunden).
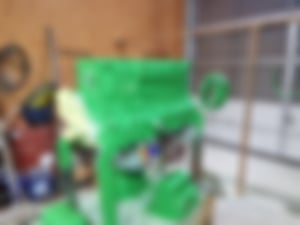
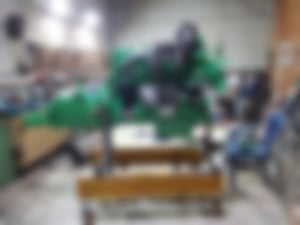
2 weitere Bilder
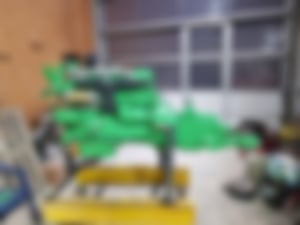
Nun ging es am Fahrerhaus weiter. Leider musste ich den ganzen Boden neu anfertigen. Für die Innenkotflügel habe ich eine Papierschablone angefertigt und dann auf das neue Blech aufgelegt und abgezeichnet. Aber leider konnte ich es nicht so biegen, wie ich es mir vorstellte. Ich musste sie 3-mal anfertigen bis sie passten. Beim Blechkanten musste ich es auch zwei oder dreimal kanten bis es passte. Die Bleche habe ich immer mit Punktschweißen stumpf angeschweißt. Die Schweißnähte habe ich alle verzinnt und danach verspachtelt. Nach ca. einem ¾ Jahr konnte ich das Fahrerhaus grundieren und auf das Fahrgestell montieren.
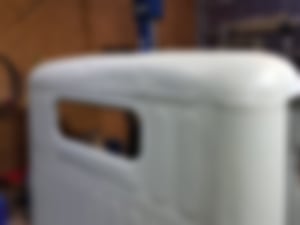
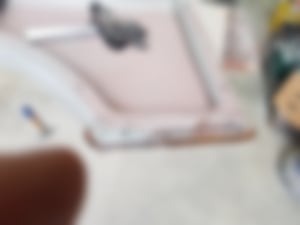
7 weitere Bilder
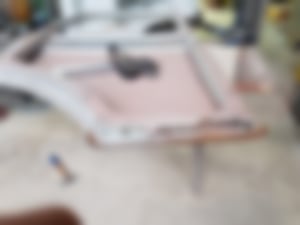
An der vorderen Stoßstange musste ich das obere Blech austauschen und die Stoßstange ausbeulen. Danach habe ich sie auch grundiert und angeschraubt.
Beim Kühlergrill trennte ich zuerst das Gitter raus. Danach kantete und bog ich die unteren Ecken und schweißte sie. Den unteren Steg musste ich komplett neu anfertigen und einschweißen. Am Oberteil brauchte ich nur zwei kleinere Blechteile einschweißen. Nun wurden alle Schweißnähte wieder verzinnt und verspachtelt. Anschließend lötete ich das ausgerichtete Gitter wieder ein und grundierte den Kühlergrill.
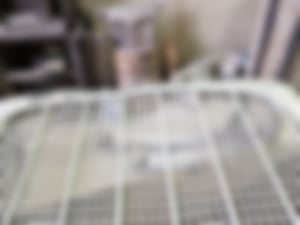
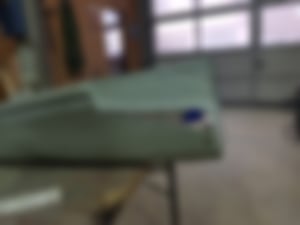
4 weitere Bilder
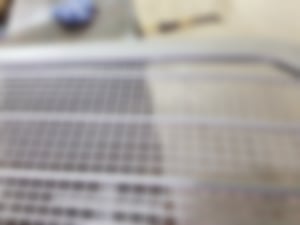
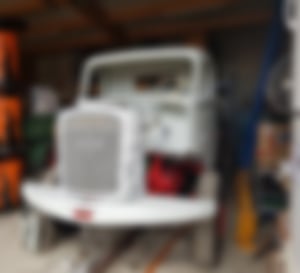
Als ich mir die beiden Motorhauben-Bleche anschaute, musste ich leider feststellen, dass diese nicht mehr zu reparieren waren.
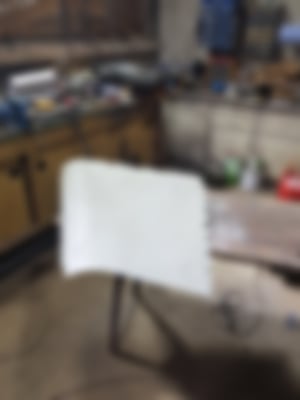
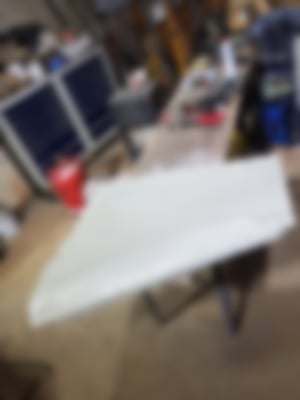
Ich fertigte mir deshalb eine Schablone an, mit der ich die Maße auf ein neues Blech übertragen konnte. Danach schnitt ich das Blech aus.
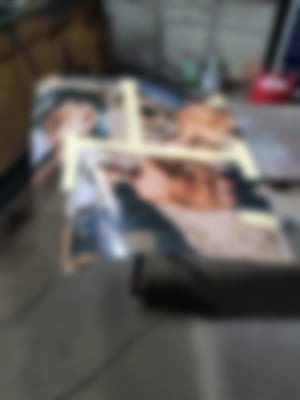
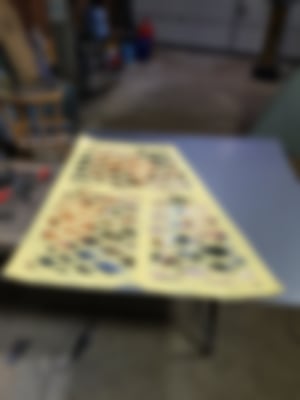
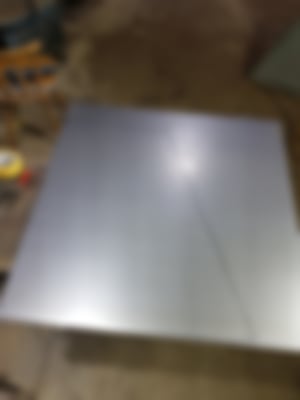
Für die Biegung zeichnete ich zuerst die Maße auf das Blech, klemmte es zwischen Tisch und einem Metallrohr und konnte es so entsprechend zurechtbiegen. Bis das Blech richtig passte habe ich es öfters am Lkw angelegt und wieder etwas mehr oder weniger gebogen.
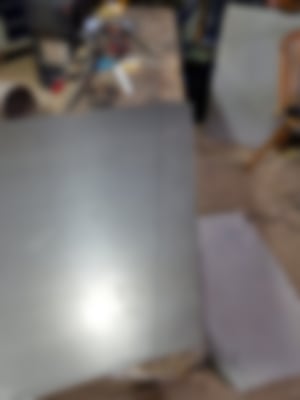
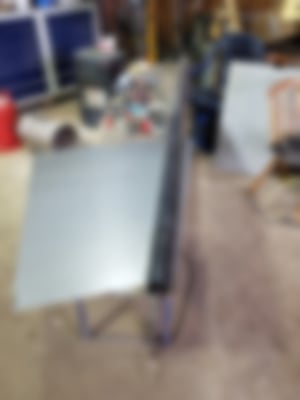
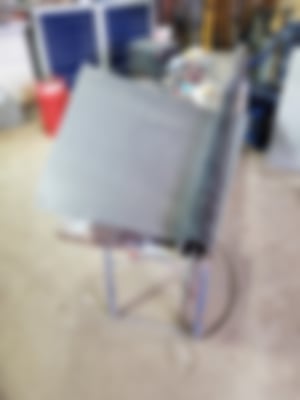
Als das Blech dann richtig passte, habe ich die Leiste gekantet und gebohrt, so dass ich sie seitlich an das Blech anschweißen (Punktschweißen) konnte.
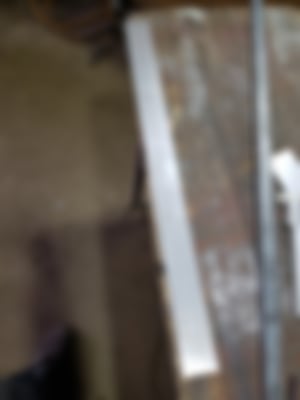
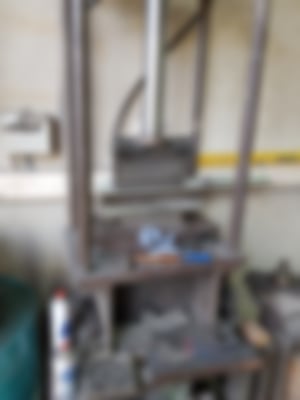
5 weitere Bilder
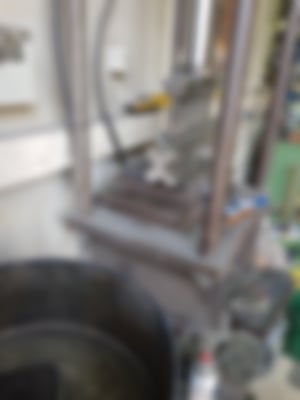